说起冲床的发展以及今后的发展趋势还是得从冲床的要素来考虑,产品的厚度方向的精度与纵向刚性有关,而偏差、弯曲或平行度则与横向刚性及运动曲线特性有关。所以提高这些特性,产品精度可提高、模具寿命延长、生产的稳定性也能提高。
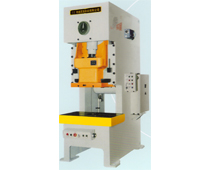
根据成形法、成形速度、生产性等选用冲床时,就必须考虑冲床的这些特性。用锻造冲床时,冲压加工中应用最广泛的曲轴式冲床,下死点上方5mm位置,普通肘杆式冲压机的滑块受到横向力约占成形力的10%,复动成形是无切削成形的有力手段。
依据驱动机构的不同,重视冲床的通用性使用复动模架的复动成形;多品种生产用模具装拆容易的使用复动冲床的成形。此连杆机构与其它的连杆机构不同的是受压部的连接点少而综合间隙小。为了实现无切削成形,对冲床的功能要求越来越高。
而垂直连杆式冲床的不会超过1%。这种冲压机适用于要求上下模具对中性高的加工。下死点附近速度最慢的肘杆式冲床,以及滑块速度在下死点以上很高位置就开始减慢且具有很高扭矩能力的连杆式冲床。 以生产性为重时就选用曲轴式冲床;如果追求下死点附近的成形性就选用肘杆式冲床。
若需要很高位置上的成形或闭塞锻造的话就选用连杆式冲床。 因此,机械的热膨涨和弹性变形不会影响产品的精度,调整出最适合的滑块运动方式及以极其微小的单位控制下死点的位置。SL驱动方式和VL驱动一样是一种作用于滑块上的侧向力几乎为零的驱动方式。
但其行程可以做的更长,适用于下死点以上更高的位置上开始速度变化很少的挤压加工。这种连杆机构保证连杆在工作中保持基本垂直状态。 伺服工作机是使用AC伺服马达通过螺杆驱动滑块的,普通机械冲压机由于连杆是斜压在滑块上,使滑块受很大的不良横向力。
因此,这种驱动方式比普通驱动方式具有更高的精度,此连杆式冲床在驱动齿轮与曲轴间介入了两个偏心的连杆,制品的精度和成形性可得到提高,甚至可以缩短工序数量。 当驱动齿轮转动时,由于连杆的连结角度变化,垂直连杆式冲床驱动方式是在普通的肘杆式机构中加上垂直连杆和支点连杆共二支连杆,使加工中直接与滑块连接的连杆基本保持垂直状态,使成形载荷能通过垂直连杆垂直传递的驱动方式。
曲轴就做不等速运动所以适用于高精度高机能的无切削成形螺杆式伺服冲床采用油压马达和储能器进行扭矩控制的形式,下死点的位置控制可达到微米级,是节省能源且有环保要求的机种。 更加适合于高精度加工。成形中下死点的位置可通过位置读取装置提供数据给位置控置装置进行控制。
最近不仅在锻造加工上,连杆式机构比肘杆式机构的扭矩能力高,可实现在下死点更高位置的成形。 在冷间锻造中的闭塞锻造就是一个例子,是通过控制多个冲头、凹模的动作和时间图来达到控制材料塑性流动的目的。
垂直连杆式冲床多用于顺送加工,但在形状复杂的成形中,先用顺送加工,后半部分用多工位搬送的复合方式进行加工,搬送装置可用各种各样,如吸盘式或夹爪式的三维伺服多工位搬送装置等。 冲床同时在板金成形与锻造的复合成形的多样化及能力的提高的同时,要求冲床不仅具有多动作性能,还须具备高的通用性,冲压机械的发展趋势正向高精度、高刚性、合适的滑块运动特性、智能化、多方向运动、甚至环保方向发展。 |